
Tube and coil for ethylene cracking furnace
Product Category:Petrochemical IndustryPrice:Negotiation
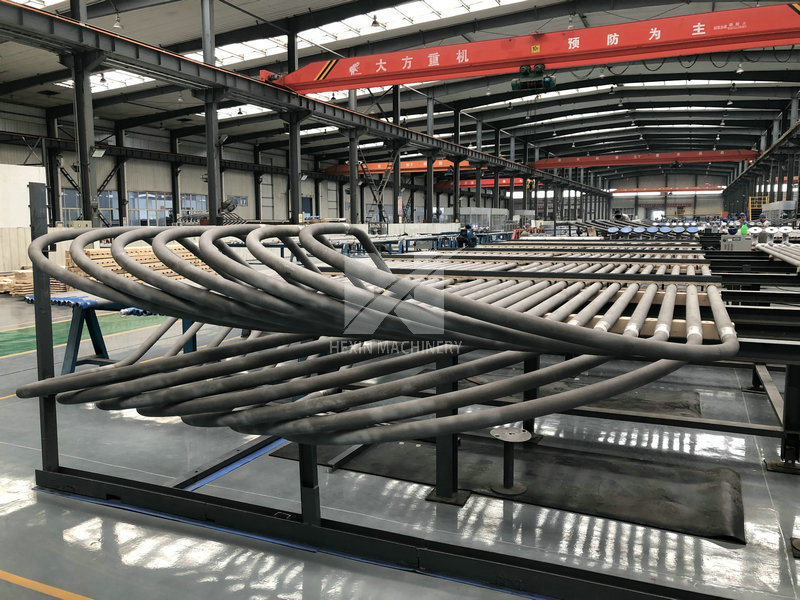
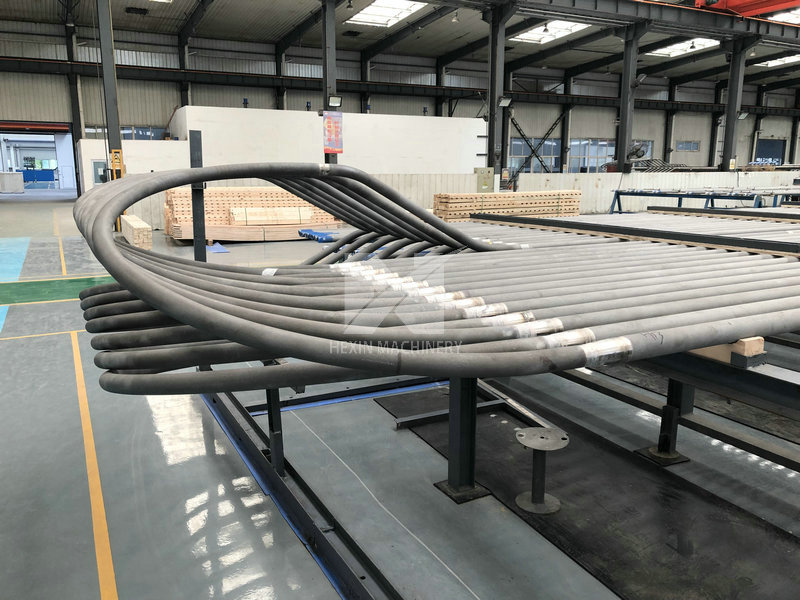
Tube cracking furnace is the main technology for ethylene production today. The cracking tube is used in the radiant section, also known as the radiant section furnace tube. The cracking tube is arranged in the radiation chamber, and a certain number of burner cracks are installed on the furnace side wall and furnace top or furnace bottom of the radiation chamber. The working temperature of the cracking tube is 1000°C-1150°C, and it is an important equipment for ethylene cracking furnace. The furnace tube components of the radiant section of the ethylene cracking furnace mainly include centrifugal casting tubes, centrifugal casting tube bends, static casting tube fittings, forgings and other components. Using the metal centrifugal casting process, the conversion tube and the ethylene cracking tube are formed by boring the inner hole, machining the welding groove on a lathe, and assembling and welding.
Our production and technical team has nearly 30 years of experience in this industry, and has the ability to produce a furnace tube for an ethylene cracking furnace with an annual output of 1 million tons per month. To manufacture these components, we strictly follow the following international standards for centrifugal casting and static casting:
Centrifugal casting: HG/T 2601, ASTM A608, DIN 10295, JIS G5122
Static casting: HG/T 3673, ASTM A351
The material grades are strictly in accordance with the standards of customers in different countries. The commonly used material grades are:
ZG40Cr25Ni35Nb, ZG40Cr35Ni45Nb, HP-Nb, HT50, GX40NiCrSiNb35-26, GX40NiCrNb45-35, SCH24XNb, etc.
Centrifugal casting tube supply specifications:
Cracking furnace tube: outer diameter 50mm-200mm, wall thickness 5mm-20mm;
Air collecting pipe: outer diameter 100mm-400mm, wall thickness 10mm-40mm;
Static casting supply specifications:
90° elbow, 180° elbow, tee pipe, palm pipe, special-shaped three-dimensional elbow, hanging parts, etc.
The tube and coil for ethylene cracking furnace is suitable for cracking furnaces, which are to be used to carry out the cracking reaction of hydrocarbons.
The typical requirement to the cracking furnace is:
1. the reactant can be quickly heated to 700~90CTC to ensure the equilibrium yield of ethylene, and heat supply and heat transfer need to be guaranteed;
2. the medium residence time is short, reducing the coke in the cracking process
3. suitable high temperature resistant materials.
Due to the differences in the raw materials used for cracking and the method of providing the heat required for cracking, different types of cracking furnaces are used, such as regenerative cracking furnaces, sand furnaces and tubular cracking furnaces.
The most widely used and the most mature technology is the tubular cracking furnace.
In the past, the cracking tube generally use HK-40 alloy steel containing 20% ??nickel and 25% chromium as the material of the cracking reaction tube, which can withstand high temperature of 1050 °C.
Due to the technical requirements to further improve the thermal strength of the furnace tube surface, after the 1970s, HP-40 alloy steel containing 35% nickel and 25% chromium was used, which can withstand high temperatures of 1100 °C.
The diameter of the reaction tube is 2-7in (1in is equal to 2.54cm), it is made by centrifugal casting, and the interior is machined flat to reduce coking during the reaction.