
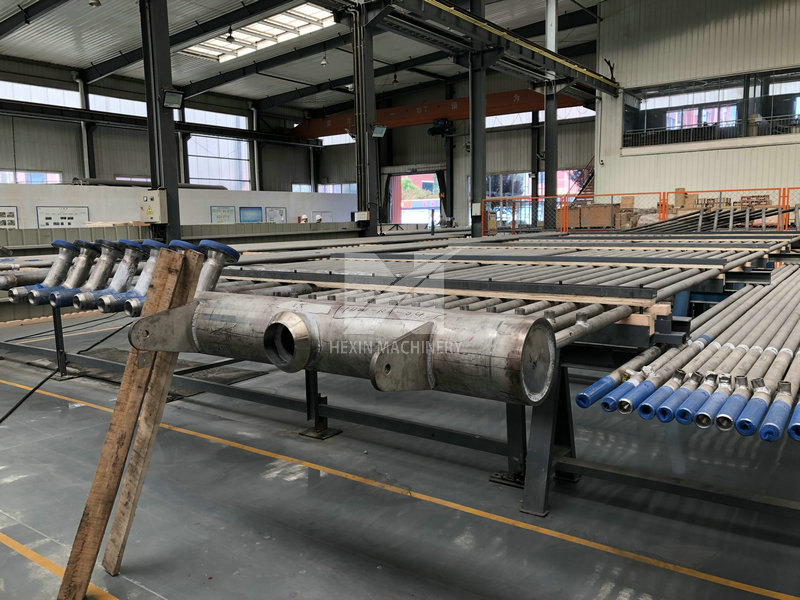
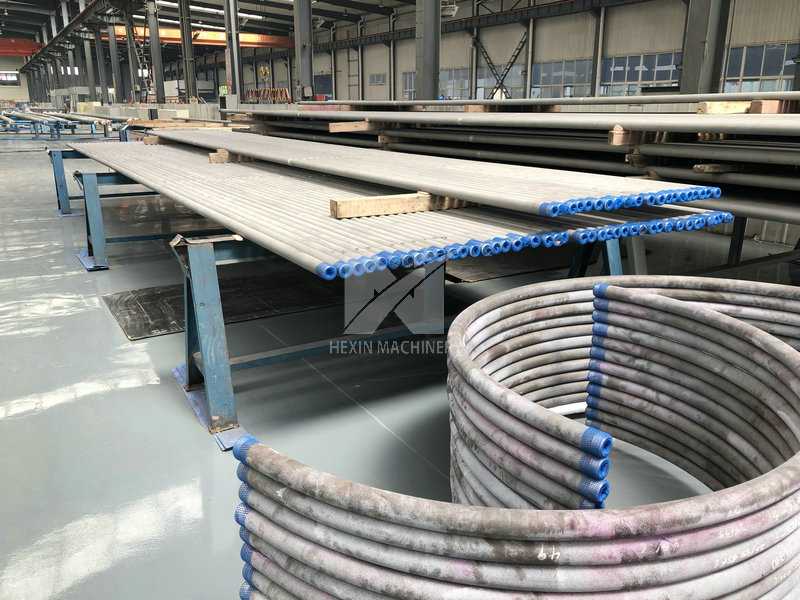
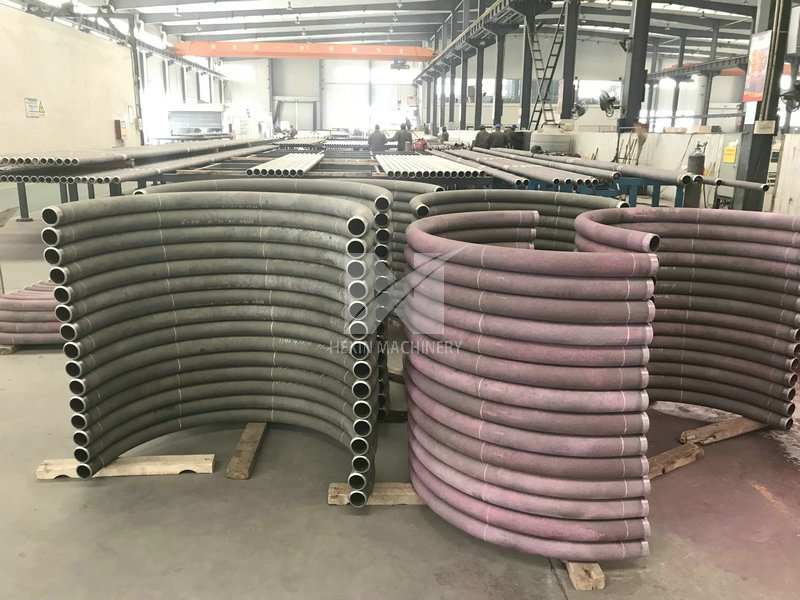
Petrochemical cracking tubes are suitable for cracking furnaces, which refer to equipment used to crack hydrocarbons. The requirement to cracking furnace is: (1) reactant can be heated to 700~90CTC rapidly, to guarantee ethylene equilibrium yield, and need guarantee heat supply and heat transfer;
(2) The residence time of the medium is short, reducing the formation of coke during the cracking process; (3) Suitable high temperature resistant materials. Due to the difference in the raw materials used for cracking and the methods of providing the heat required for cracking, different cracking furnace types are used, and the commonly used ones are regenerative cracking furnaces, sand furnaces and tubular cracking furnaces. The most widely used and most mature technology is the tube cracking furnace.
In the past, cracking tubes generally used HK-40 alloy steel with 20% nickel and 25% chromium as the cracking reaction tube material, which can withstand high temperatures of 1050°C.
Due to the process requirements to further increase the heat intensity of the furnace tube surface, after the 1970s, HP-40 alloy steel containing 35% nickel and 25% chromium was used, which can withstand high temperatures of 1100 °C. The diameter of the reaction tube is 2-7in (1in is equal to 2.54cm), which is made by centrifugal casting method, and the inside is machined to reduce coking during the reaction process.