
Coated rollers with plasma spray coating
Product Category:Metallurgical IndustryPrice:Negotiation
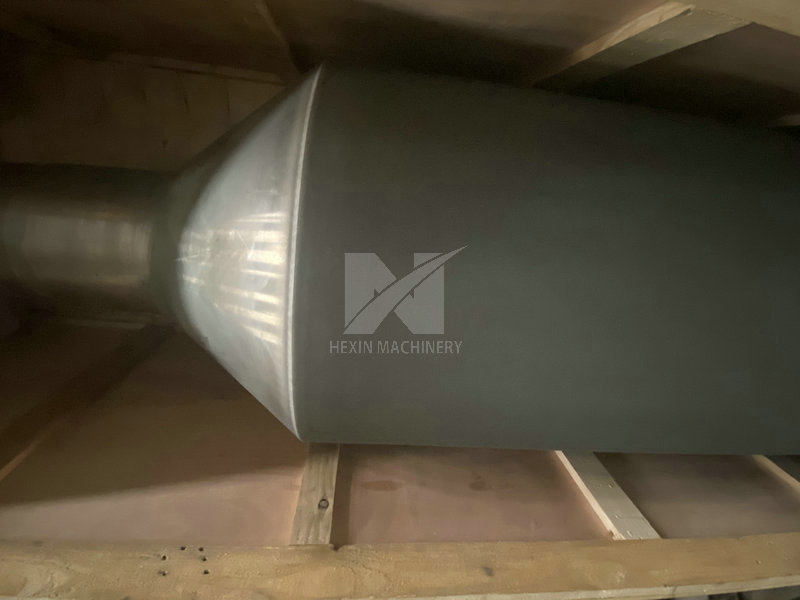
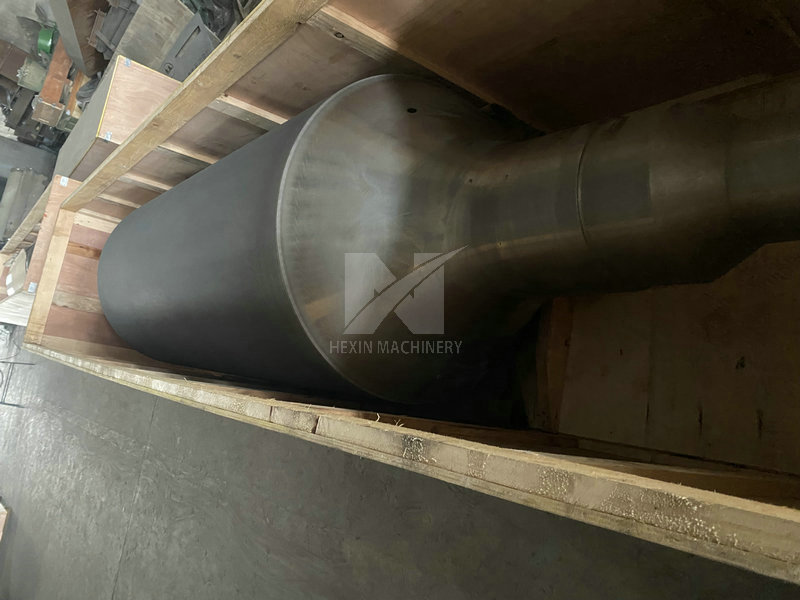
Spraying furnace roll is to form a surface coating on the surface of the furnace roll by spraying, surfacing and other surface composite methods, so as to improve the wear resistance, corrosion resistance and high temperature oxidation resistance of the furnace roll, and improve the life of the furnace roll and the stability of the production line. We have many years of experience in producing spray furnace rollers.
Coated furnace rolls are mostly used in vertical annealing furnaces for high-end automotive panels, home appliance panels, and galvanizing lines. Under a nitrogen-hydrogen protective atmosphere, the surface of the furnace rolls can be sprayed with various special coatings at a temperature of 750 In the -950 degree furnace, the steel belt is uniformly and quickly conveyed to complete the annealing process; the diameter is 600-1500mm, the surface coating of the furnace roller improves the surface hardness of the furnace roller, and the surface of the furnace roller is more stable during use, which greatly reduces surface scratches. Improve the quality of the board.
Coated furnace rolls are mostly used in vertical annealing furnaces for high-end automotive panels, home appliance panels, and galvanizing lines. The surface coating improves the surface hardness of the furnace rolls. The surface of the furnace rolls is more stable during use, which greatly reduces surface scratches. Improve the quality of the board.
Commonly used coatings: LC1C, WC, LCO56, LCO117, etc.
The coating of the sprayed furnace roll can be designed, developed and manufactured according to different working conditions. For example, tungsten carbide coated rollers are widely used in various transmission systems such as papermaking industry, metallurgical iron and steel industry, mining transportation equipment and packaging printing machinery. Due to the high speed, high temperature, heavy load or corrosion of mechanical equipment in various industries Operating in the environment, the wear, scratches, corrosion and oxidation of various rollers of its mechanical equipment are serious, which gradually leads to the failure of parts. The surface of the roller is modified by thermal spraying technology, and the spraying of tungsten carbide coating can make the roller repair the old one better than the new one, and prolong the life of the roller with high energy. Wear resistance, also known as wear resistance, refers to the ability of materials to resist mechanical wear, and the wear resistance of materials. Wear resistance is related to almost all properties of materials, and under different wear mechanism conditions, there are different requirements for material properties in order to improve wear resistance. The hardness of the tungsten carbide wear-resistant coating is only lower than that of diamond, and the roller sprayed with tungsten carbide coating can effectively solve the wear problem. Spraying the tungsten carbide coating on the roller can make the workpiece have good wear resistance and corrosion resistance, heat resistance and heat insulation, insulation and other characteristics that the base material does not have, and extend the service life several times to dozens of times. While saving a large amount of materials, it also exerts excellent performance that cannot be compared with conventional and other special processing. Due to the superior performance of the rollers, the inventory of materials and spare parts can be saved, the downtime rate can be greatly reduced, and economic benefits can be improved.
Hexin pay special attention for the production of the coated rolls.
The main technology used in spraying furnace rolls is spray welding technology, which uses oxyacetylene flame as a heat source, sprays self-fluxing alloy powder onto the surface of pretreated furnace rolls, and then heats the coating to melt and wet the furnace. The surface of the roller, through the mutual dissolution and diffusion of the liquid alloy and the solid surface of the furnace roller, realizes the metallurgical combination and forms the processing technology of the dense spray welding layer.
Generally speaking, the coated furnace roll has a functional protective coating with high density, high hardness and high bonding strength, which has excellent properties such as wear resistance, corrosion resistance and heat resistance, and effectively prolongs the service life of the furnace roll , Improve the economic benefits of the production line.