
The development of conversion furnace tube
Product Category:Industry NewsPrice:Negotiation
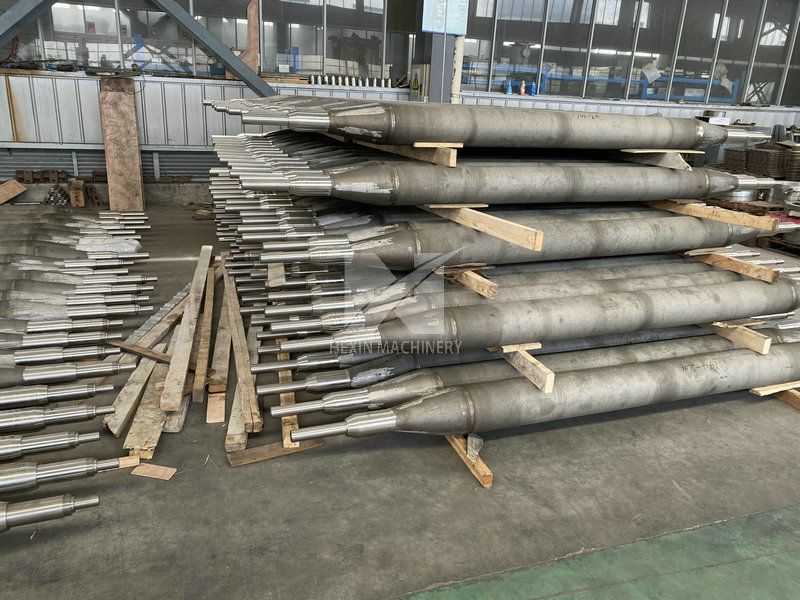
The development of conversion furnace tube materials has gone through several stages. The earliest material used was the 18Cr/8Ni series, which was not used at high temperatures and pressures (ensuring heat resistance below 600 ℃). Later, multiple adjustment tests were conducted on the composition of Cr and Ni, and it was found that the thermal strength of 25Cr20Ni was relatively good. To further improve its strength, the mass fraction of C was increased from 0.1% to 0.4%, and HK-40 high-temperature centrifugal casting furnace tube was developed as the conversion tube. In the 1960s and 1970s, almost all hydrocarbon steam conversion pipes used HK-40. The original conversion furnace tube did not process inner holes, with a wall thickness of up to 22mm and uneven thickness. This not only resulted in high internal stress and material weight of the furnace tube, but also high cost and low thermal efficiency, resulting in low medium conversion efficiency. Although the inner holes were improved after processing, and after using it for a period of time, it was found that operating HK-40 in the temperature range of around 800 ℃ is prone to harmful effects σ Phase. To reduce σ Xiangsheng, later produced an improved version of HK-40mod.
In the 1980s, HP series high-temperature alloys, which were used as materials for ethylene cracking furnace tubes, were also used for hydrocarbon steam reforming furnaces. HP heat-resistant alloys were developed based on the HK series, with a 15% increase in Ni mass fraction. Ni is an element that strongly forms and stabilizes austenite and expands the austenite phase zone. In austenitic stainless steel, as the nickel content increases σ The tendency towards phase formation is significantly reduced. Under the same carbon content, HP has more eutectic carbides than HK, thus increasing the creep fracture strength. The maximum operating temperature of this steel can reach 1100 ℃. In order to further improve the high-temperature creep fracture strength and high-temperature toughness of the furnace tube, alloy elements such as Nb, W, Mo, and Ti were added to HP, forming a series of alloy furnace tube steel grades. Among them, HP-40Nb is currently the material commonly used in hydrogen production conversion furnaces.
HP-40Nb contains Nb and W, while HK-40 does not contain these two elements. The Nb and W elements can improve the carburization property of the material, increase the crack resistance when the temperature changes dramatically, and thus improve the high-temperature toughness of the material. The HP-40Nb linear expansion coefficient is smaller than HK-40, while the thermal conductivity coefficient is higher than HK-40, thus improving the thermal shock resistance of the material. In addition, the element Nb in HP-40Nb can generate small and uniformly distributed Nb (C and N) compounds in the alloy matrix, greatly improving the high-temperature creep strength of the alloy. The high-temperature strength at 1000 ℃ is about 80% higher than that of HK-40.