
Methods for extending the service life of furnace tubes
Product Category:Industry NewsPrice:Negotiation
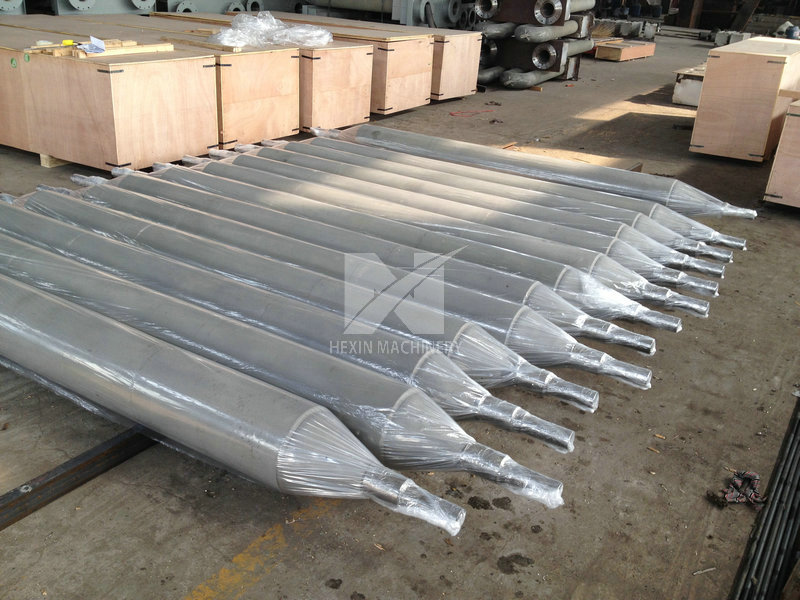
Methods for extending the service life of furnace tubes
1. Control furnace tube overheating
In order to prevent overheating from causing damage to the furnace tube, the following control measures can be taken for various reasons.
(1) Strict management and scientific loading of catalysts during loading. First, place the catalyst in a long cloth bag and slowly deliver the bag along the pipe wall
At the bottom of the furnace tube, remove the cloth bag from the furnace tube to prevent bridging and pulverization of the catalyst. Before and after catalyst loading
Measure the pressure difference of each furnace tube to ensure that the pressure drop is maintained within ± 5% of the average pressure drop of the furnace tube, ensuring uniform fluid distribution
Uniform.
(2) Control a suitable and stable vapor carbon ratio, maintain its upper limit as much as possible, and not less than 3. High vapor carbon ratio can suppress catalyst deposition
Carbon reactions occur and prevent methane and light hydrocarbons from accumulating carbon in the tube.
(3) Maintain the activity of the catalyst. This not only directly affects the conversion rate, but also directly affects the service life of the conversion tube. In very
To a large extent, the tube wall temperature is the most direct and reliable ruler for measuring the condition of catalysts. In the case of poor catalyst activity,
It should be replaced as soon as possible to avoid using the method of increasing furnace temperature to compensate for the shortcomings of the catalyst.
(4) Strengthen burner management. Control the temperature difference between single pipes within 30 ℃, and carry out desulfurization, deoiling, and dehydration work before the gas enters the furnace
To reduce the corrosion of gas on furnace tubes. Ensure that the burner is flat, short, and even, firmly eliminate large flames, and ensure frequent inspection, repair
Frequent inspection.
(5) The design of the conversion tube should be reasonably configured according to the specific situation.
(6) Strictly control various process indicators, achieve stable production, and minimize the number of starts and stops to prevent thermal fatigue.
2. Quality inspection of purchased furnace tubes
Outsourced furnace tubes should be inspected properly. It is recommended to purchase pipes with unprocessed outer walls to ensure excellent casting structure. Simultaneous pipe section
The entire wall thickness should be a dense layer organization, and the inner container should be carefully processed without leaving any casting defects such as inclusions and shrinkage holes to prevent
Carburization.
3. Update and replacement of furnace tubes
By changing the chemical composition of the furnace tube, the high-temperature resistance and creep resistance of the furnace tube can be improved. HK-40VH has been developed domestically
New improved alloys such as HP40-Nb have significantly better performance than HK-40 furnace tubes.