
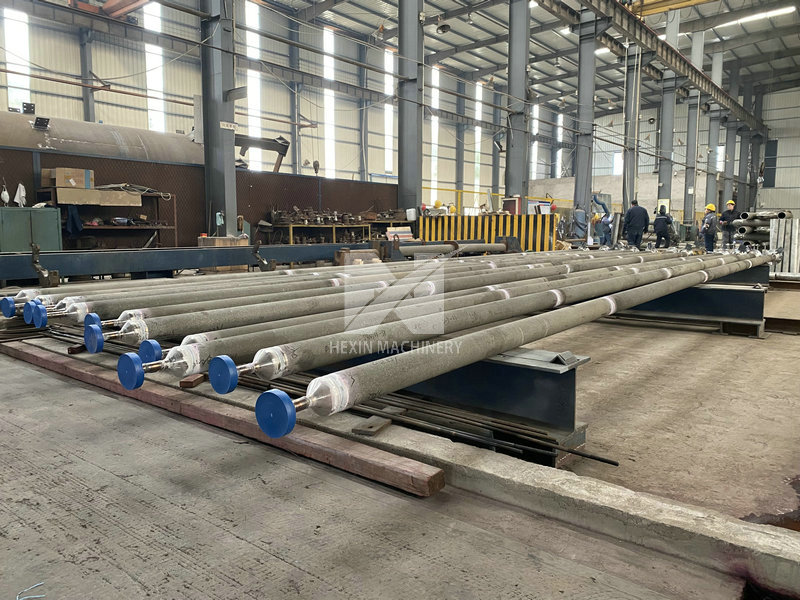

Reformer Furnace Tubes
Furnace tube for hydrocarbon steam reforming hydrogen production device, hydrocarbon steam reforming hydrogen production device, the equipment mainly includes: inlet gas header, reformer tube, outlet gas header, upper and lower pigtail pipes, etc. Among them, the reformer tube is produced by centrifugal casting process, and the working temperature is 900℃-1000℃, which is an important equipment of hydrogen production reformer.
Our production and technical team has nearly 30 years of experience in the industry and has the ability to produce 500 reformer tubes per month. To manufacture these parts, we strictly follow the following international standards for centrifugal casting and static casting:
Centrifugal casting: HG/T 2601, ASTM A608, DIN 10295, JIS G5122
Static casting: HG/T 3673, ASTM A351
The material grades are strictly in accordance with the standards of customers in different countries.
The typical material grades are:
ZG40Cr25Ni35Nb, ZG40Cr35Ni45Nb, HP-Nb, HT50, GX40NiCrSiNb35-26, GX40NiCrNb45-35, G-NiCr28W, SCH24XNb
Specifications of conventional centrifugal casting products:
Reformer tube: outer diameter 100mm-300mm, wall thickness 8mm-20mm;
Hot wall gas collector: outer diameter 100mm-400mm, wall thickness 10mm-40mm;
The development of reformer furnace tube materials has gone through several stages. The earliest material used is the 18Cr/8Ni series, and the temperature and pressure used are not high (the heat resistance strength is guaranteed below 600 °C). After adjusting the test, it was found that the thermal strength of 25Cr20Ni was better. In order to further improve its strength, the content of C was increased from 0.1% to 0.4%, and the HK-40 high temperature centrifugal casting protective tube was developed as a conversion tube.
In the 1960s and 1970s, HK-40 was almost always used in the combustion-type steam reforming tubes. The original reforming furnace tube did not have inner holes, and the tube wall was as thick as 22mm, and the thickness was not uniform, which not only made the internal stress of the furnace tube large and the weight of the material, but also kept the cost high and the thermal efficiency low, resulting in medium conversion efficiency. Low, although the inner hole has been improved after processing. And after using for a period of time, it is found that HK-40 is easy to produce harmful σ phase in the temperature range of about 800℃.
In order to reduce the generation of σ phase, an improved HK-40mod was produced later.
During the 1980s, HP series superalloys used for ethylene cracking furnace tube materials were used in hydrocarbon steam reformers. HP heat-resistant alloy is developed on the basis of HK series, in which the content of Ni is increased by 15%. Ni is an element that strongly forms and stabilizes austenite and expands the austenite phase region. In austenitic stainless steel, with As the nickel content increases, the tendency to form σ phase decreases significantly.
Under the same carbon content, HP has more eutectic carbides than HK, so the creep rupture strength is improved, and the maximum service temperature of this steel can reach 1100 °C. In order to further improve the high temperature end-change fracture strength and high temperature toughness of the furnace tube, Nb, W, Mo, Ti and other alloy elements were added on the basis of HP to form a series of sensitive grades of alloy furnace tubes. Among them, HP40-Nb is the most commonly used material in hydrogen production reformers.
The reformer tube adopts the structural form of lower support and upward expansion, and its weight is suspended by the spring set in the furnace to reduce the stress of the piping system in the hot state. There are two upper gas collecting pipes on the upper part of the reformer tube, which are connected with the reforming tube through the upper tail pipe. The upper tail pipe is used to compensate the displacement in different directions between the upper gas collector and the conversion pipe.
Due to the low working temperature (450~540℃) of the upper gas collecting pipe and the upper tail pipe, chrome molybdenum steel is used, and the lower part of the reformer tube is directly seated on the lower gas collecting branch pipe.