
Charging and discharging rolls for billets reheating furnace
Product Category:Metallurgical IndustryPrice:Negotiation
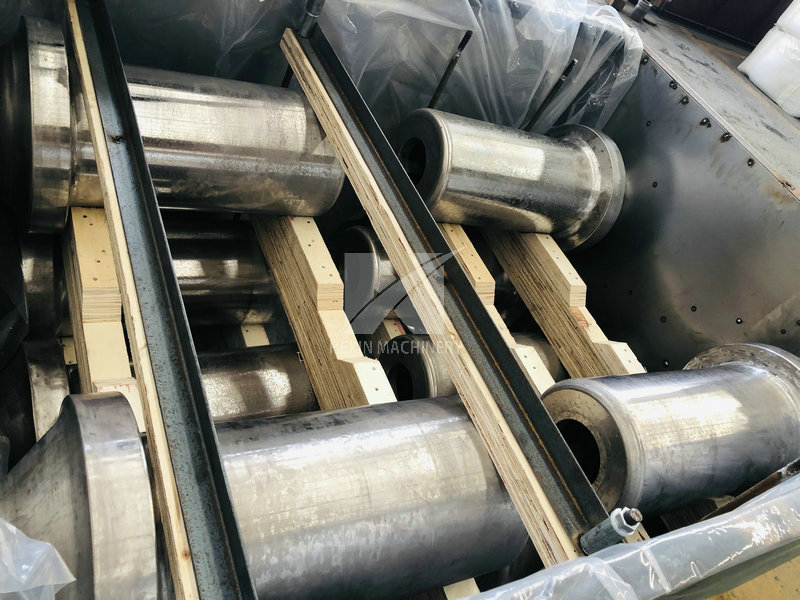
Charging and Discharging roll, are produced by static casting method, machining, heat treatment.
Some also call it cantilever rolls.
Cantilever roll is an indispensable processing equipment in the steel plate smelting production process. In order to ensure the requirements of steel plate production, the cantilever roll also has high requirements for use. Cantilever rolls are one of the important components for supporting and transporting slabs in metallurgical equipment, and they are widely used in steel plate continuous casting and rolling production lines.
The structures of the rollers and work rollers on the existing conveying cantilever rollers generally adopt integral forging, casting and welding, alloy seamless welding and other structures. During the working process of the rollers, due to the different working conditions of the upper roller body and the roller shaft , therefore, the performance requirements are different;
but the heat-resistant roller table of the existing structure is an integral or welded structure, and the material properties of each part are the same or similar, which cannot meet the performance requirements of each part of the production needs at the same time. , which leads to a shorter life of the wear-resistant roller table, frequent replacement, and higher production costs.
The support part in the middle of the cantilever roll is directly installed in the furnace, while the cone section and the bearing support part are installed in the furnace wall and outside the calcining furnace, respectively. The temperature gradient of different parts of the cantilever roll is very large, so the cantilever roll The body, the cone and the shaft are welded to each other. In order to reduce the burning loss to the inner surface of the cone, a heat shield is designed inside the cone.
In order to ensure the smooth transportation of high temperature slabs, it is required that the roller shaft is not deformed and the outer roller ring is heat-resistant and wear-resistant.
During the rolling process, the billet needs to be continuously and stably heated in the heating furnace to the rolling temperature of 1050-1150 ℃, and the stable support of the slab is realized by the bottom roller to ensure smooth and uniform transportation.
Since the middle section of the hearth roll is directly installed in the billet calcining furnace, the furnace gas temperature is as high as about 1150°C during the production process, and it is usually made of superalloy materials.
The cantilever roll discharged from a steel rolling heating furnace.
We produce cantilever roller with high temperature resistant alloy steel of nickel chrome alloy , like material: ASTM A351 HK40, 1.4848, 2.4879,1.4852.
It consists of a blind plate, a roller sleeve, a support plate, a shaft and a water inlet pipe. The roll sleeve is an integral structure. The same ends are respectively welded with a blind plate, a support plate and a shaft. The water inlet pipe enters the roller sleeve through the central hole of the shaft and the support plate. Because the utility model has the advantages of simple structure, easy manufacture, low cost and long service life, the utility model is suitable for the use of each steel rolling heating furnace. But how to choose a good cantilever roller, its material, manufacturing process, performance and life are all important factors we need to consider.
It relates to the improvement of the structure of a cantilever roller head on a walking furnace. The roller head includes a roller head and a roller shaft. The roller head sleeve is provided outside the roller shaft, and further includes a positioning sleeve and a positioning pin; the positioning sleeve is provided between the roller head and the roller shaft, and the positioning sleeve is fixed. Connected to the roller shaft; an axial positioning pin hole is provided between the outer surface of the inner end of the positioning sleeve and the inner surface of the inner end of the roller head, and the positioning pin is provided at the positioning A pin hole; the roller head is fixed circumferentially relative to the positioning sleeve; a step hole is provided at the edge of the inner port of the roller head, the retaining ring is provided in the step hole, and the inner surface of the retaining ring Fixedly connected to the roller shaft; so that the retaining ring is axially fixed relative to the roller shaft